How much does it cost to manufacture one piece of clothing?
You are facing your closet door while looking at the single t-shirt that becomes your daily wear. The expenses required to manufacture one piece of clothing remain a mystery to most people. The actual cost exceeds your store purchase price because it includes the fabric materials with their stitching process and the workers who created it. You would not expect the process to be this complex.
Clothing prices can feel like a mystery. More fitness brands invest in premium athletic clothing since they recognize the various benefits custom gym wear brings to their brand along with customer retention and design advantages for stronger motivation. Custom gym wear manufacturers are essential in providing tailored solutions to meet the growing demand for high-quality and personalized fitness apparel.
Why does one shirt cost $10 while another looks almost the same but costs $50?
Farm products turn into fashion items through a manufacturing process that exceeds basic fabric and thread contributions. The manufacturing process incorporates human effort through resources in addition to moral considerations.
The manufacturing expenses for a single clothing item make up a significant portion of your total expenditure because various elements influence this price point. Each phase starting from cotton farming to factory stitchwork amounts to higher costs.
Innovate Apparel provides detailed information about the various factors that influence the final price of your cherished t-shirt or jeans.
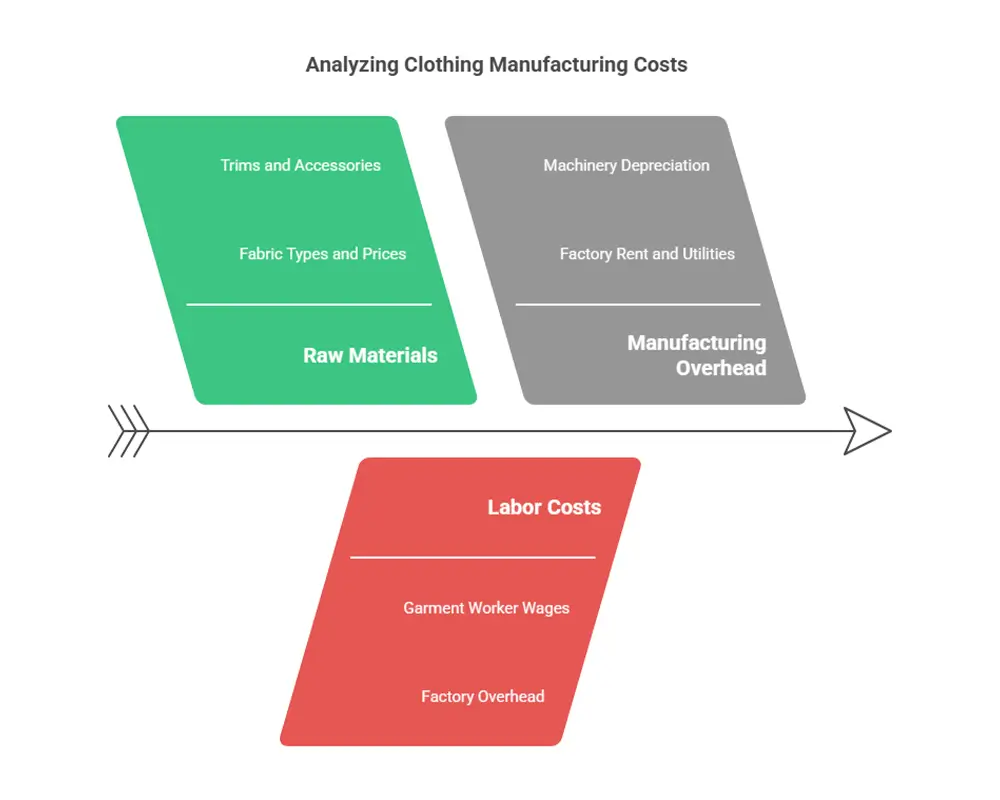
Breaking Down the Costs: Direct Costs of Manufacturing
Raw Materials Cost in Manufacturing
Types of Fabrics: Each clothing fiber including cotton and polyester and blend materials comes with unique price points. Natural feeling cotton fibers cost more money than synthetic materials such as polyester even though they have a similar soft texture. And guess what? Fabric prices can swing wildly depending on things like weather (bad cotton harvest? Prices go up) or oil prices (since synthetics are made from petroleum).
Yarn Costs: Before fabric becomes fabric, it’s yarn. Spinning fibers into yarn and dyeing them adds to the cost. Fancy colors or intricate patterns? That’s extra.
Trims and Accessories: Small items such as buttons and zippers and labels increase the overall production costs even though they seem insignificant at first. Plastic zippers exist as cheaper alternatives to metal zippers thus enabling price reduction that benefits manufacturers.
Fabric Waste: Cutting fabric into pieces for clothing leaves scraps. The more waste, the more fabric you need to buy upfront, which drives up costs.
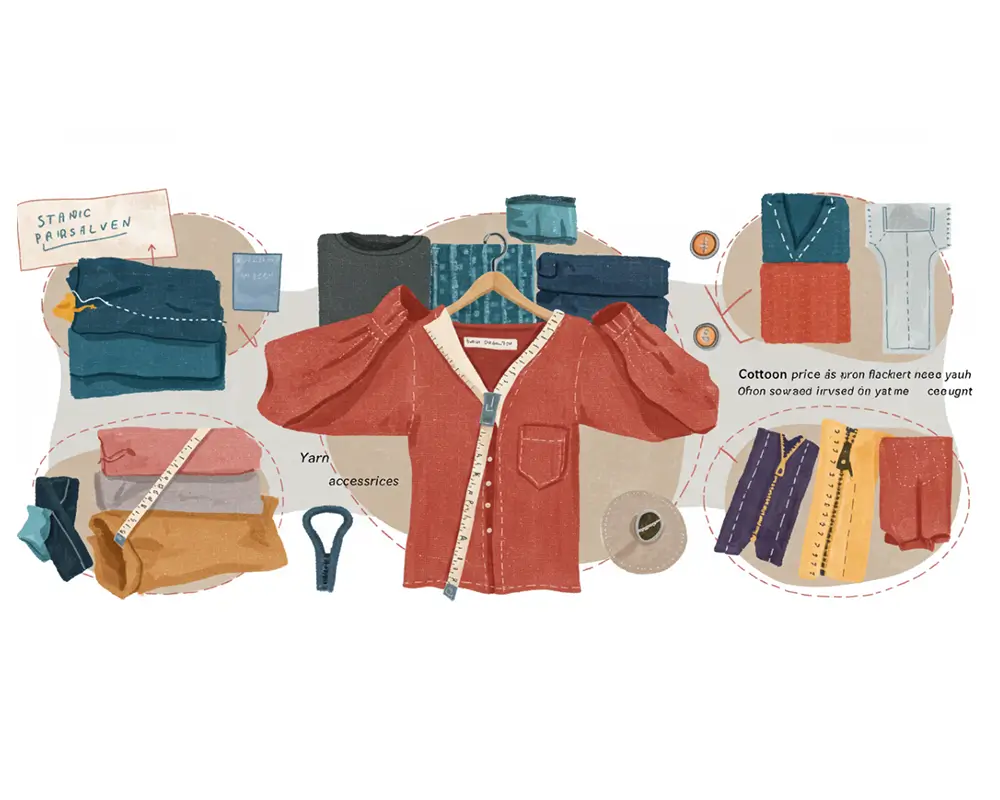
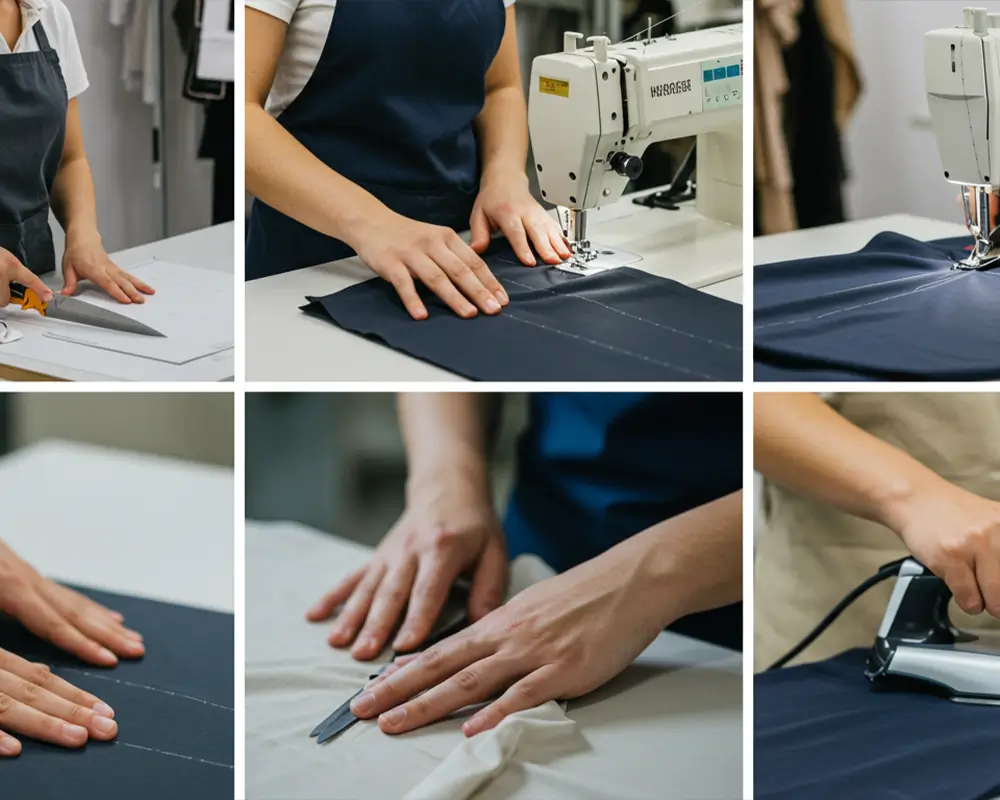
Labor Cost in Manufacturing
Now, let’s talk about the people who actually make the clothes. This is where things get complicated—and sometimes controversial.
Garment Worker Wages: Wage amounts for clothing production depend on the country of origin because workers receive either minimal daily pay or sufficient compensation based on their location. The manufacturing cost varies extensively between countries where workers receive minimum wages such as Vietnam and Bangladesh and countries like Europe and the United States which pay higher wages.
Cutting, Sewing, and Finishing: Turning fabric into clothes takes skill and time. A simple t-shirt might take minutes to sew, but a detailed dress with intricate stitching? That’s hours of work. More time = more cost.
Factory Overhead: It’s not just about wages. Factories also have to cover things like worker insurance, benefits, and safety measures. These costs get factored into the final price too.
Manufacturing Overhead Cost in Manufacturing
Running a factory isn’t cheap. Similarly, it is difficult to find activewear manufacturers or the one who is an expert manufacturer in all garments. You cannot observe all the processes that take place in the creation of a shirt when you decide to buy it.
- Factory Rent and Utilities: Industrial facilities need dimensional space combined with electrical power as well as access to clean water to maintain their production. The prices of big manufacturing facilities as well as industrial locations with elevated living expenses become more expensive.
- Machinery Depreciation and Maintenance: The durability of fixing tools and sewing devices and other manufacturing equipment is finite. The expenses of production include expected costs for equipment maintenance and repair systems and new equipment replacements.
- Quality Control and Inspection: A thorough quality check for defects happens before clothing products exit the factory premises. The expense grows because this examination demands personnel to handle it over extended periods.
- Shipping and Transportation: The finished clothing items must travel from the production area to storage locations or retail markets. Any attempt at global goods transportation through trucks, ships, and planes demands financial costs from manufacturers.
Many people fail to realize why clothes tend to be more expensive than expected because they must consider material costs and labor expenses as well as building maintenance expenses. But wait, there’s more! You can get a quick quotation from our own fitness clothing manufacturer for free.
Indirect Costs & Markups
Okay, so we’ve covered the direct costs of making clothes—materials, labor, and factory stuff. Before clothing reaches stores consumers need to cover various expenses that extend beyond manufacturing costs. Brands together with retailers implement additional expenses for the costs which operate out of sight.
Design and Development
Costs arise from each piece of clothing because designers create initial designs for production. Creativity-driven payment to designers is required for sketches which after refinement pattern makers convert into workshop templates for production. Before mass production, brands create samples to test the design, often requiring multiple revisions. Additionally, tech packs and production specs—detailed instructions for factories—ensure consistency but add to expenses.
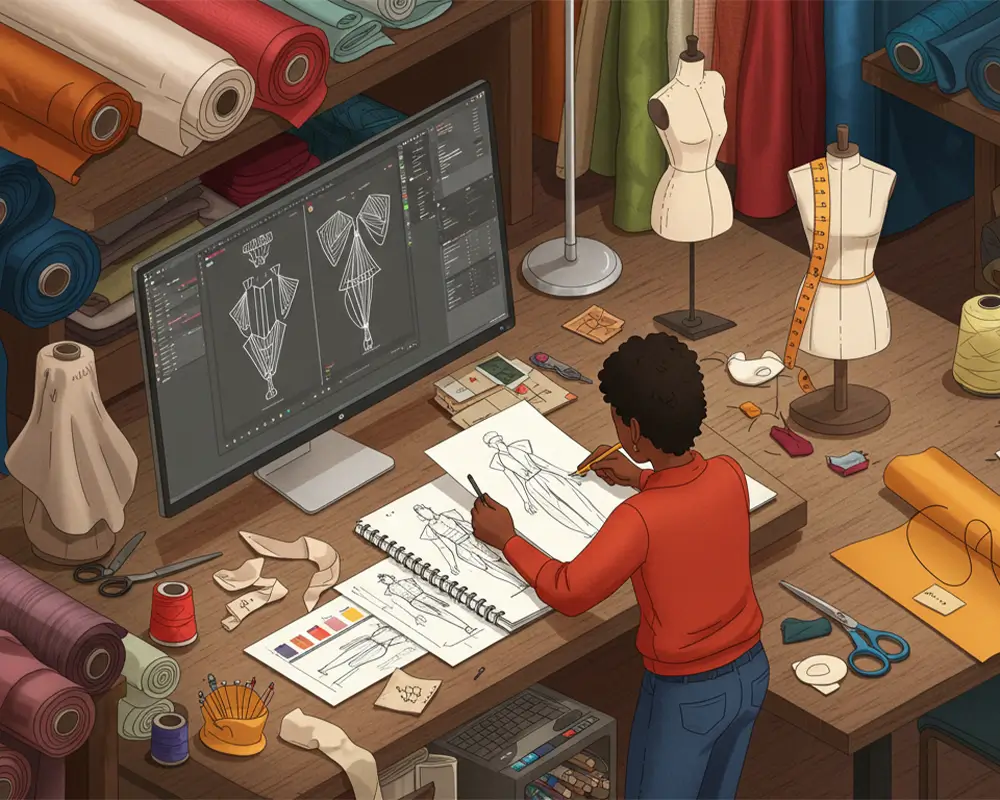
Marketing and Distribution
Brand Premium
Profit Margins
Takeaway - Cost to Manufacture One Piece of Clothing?
The actual expenses involved in manufacturing one piece of clothing remain an important question to answer. All clothing production stems from its inherent materials together with workforce expenses, facility expenses and design costs, marketing expenses, and brand worth calculation. Manufacturing location together with the process combined with manufacturing workers influence the end price of products.
Understanding these manufacturing expenses allows you to view the complete system rather than only be puzzled about high-priced jeans. Each purchase you make stands for a particular operational model that prioritizes sustainability or discounts the cost for customers.
As consumers, we possess the ability to get the system to deliver enhanced working conditions with improved environmental operations and superior product quality. Examine the history of your chosen t-shirt when you hold it the next time. Fashion extends beyond clothes since it determines the choices you want to make in the world.